The Ultimate Guide to Dacromet Coating: Superior Protection for Fasteners and Construction Components
Introduction: What Is Dacromet Coating and Why Is It Essential?
Metal parts, especially fasteners and construction components, are highly susceptible to rust and corrosion, leading to costly replacements and repairs. Traditional coatings often fail under harsh conditions. Dacromet coating offers unmatched corrosion resistance, making it a top choice for industries like construction and automotive.
Read on to discover how this innovative coating technology can extend the lifespan of your parts and reduce long-term maintenance costs.
What Is Dacromet Coating?
The Science Behind Dacromet Coating
Dacromet is an aqueous-based coating composed of zinc flakes, aluminum powder, and inorganic compounds. It creates a multi-layer protective barrier, significantly enhancing corrosion resistance for fasteners and construction hardware.
How It Works
Immersion & Rotation – Parts are immersed in the coating solution and rotated for uniform coverage.
Curing Treatment – The coating is cured at high temperatures, forming a 7-8 µm thick protective layer.
Protection Mechanism:
Zinc Flakes – Act as a sacrificial anode, preventing corrosion.
Aluminum Flakes – Form a durable barrier against environmental elements.
Inorganic Binder – Secures the metal particles for long-lasting protection.
Types of Dacromet Coatings: Which One Is Right for You?
Standard Dacromet Coating (with Hexavalent Chromium)
310/320 – Ideal for fasteners and spring components in construction applications.
500 – Suitable for high-performance automotive and wind energy parts.
Geomet Series (Chromium-Free, Eco-Friendly Options)
720 – Excellent for fasteners and automotive parts.
321 – Provides enhanced reliability for construction hardware.
500 – Self-lubricating, ideal for fasteners in construction projects.
320/360 – High-temperature resistance, suitable for automotive and construction parts.
Dacromet Coating Process: The Key to Superior Durability
Core Materials Used in Dacromet Coating
Zinc Flakes – The primary corrosion-resistant material.
Aluminum Powder – Enhances the coating’s protective barrier.
Inorganic Binder – Improves adhesion and coating integrity.
Additives & Water Carrier – Ensure even coverage, particularly for fasteners.
Step-by-Step Process for Dacromet Coating
Surface Pre-Treatment
Cleaning and contaminant removal.
Sandblasting or chemical treatment for better adhesion.
Coating Application
Immersion in the coating solution with controlled rotation.
Air drying before curing.
Curing Process
Heated to approximately 300°C for optimal curing.
Controlled cooling to prevent cracking.
Key Benefits of Dacromet Coating: Why It’s a Game Changer
Unmatched Corrosion Resistance
Withstands 1,000+ hours of salt spray testing.
Prevents red rust formation, ideal for extreme conditions.
Enhanced Durability and Longevity
Dacromet-coated parts can last 20+ years.
High adhesion and wear resistance extend component lifespan.
Impressive High-Temperature Performance
Stable up to 300°C, making it suitable for construction and automotive parts.
Environmentally Friendly
Zero VOC emissions, making it safe for eco-conscious projects.
REACH and RoHS compliant for responsible manufacturing.
Lower Maintenance Costs
Self-healing properties prevent scratches from compromising protection.
Long-lasting durability reduces upkeep costs.
Limitations of Dacromet Coating: What You Should Know
Limited Color Options – Usually available in a gray matte finish.
Impact Sensitivity – Excessive force may damage the coating.
Longer Curing Time – Takes longer than traditional coatings.
Thickness Control – Intricate shapes may receive uneven coverage.
Higher Initial Cost – Although expensive upfront, it provides long-term savings.
Dacromet Coating Applications: Where It Makes a Difference
Automotive Industry
Brake system components
Suspension parts
Engine and chassis fasteners
Fuel system components
Aerospace and Military
Structural fasteners
Landing gear components
Ground support equipment
External hardware
Construction and Infrastructure
Bridge components
Road barriers
Construction fasteners
Structural supports
Marine Industry
Deck hardware
Offshore platforms
Container components
Port equipment
Dacromet Coating vs. Electroplated Zinc: A Side-by-Side Comparison
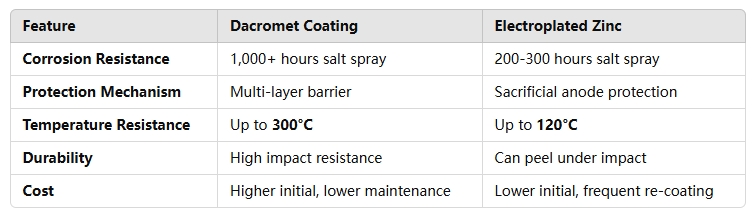
Conclusion: Make the Smart Choice for Your Construction and Automotive Parts
Dacromet coating provides unmatched protection, durability, and environmental benefits, making it the best choice for fasteners and construction hardware exposed to harsh environments. Despite a higher upfront cost, it delivers lower maintenance costs and longer service life, making it a wise investment for industries like construction, automotive, and aerospace.
If you want to learn more about Dacromet coating and how it can benefit your construction components, contact us today!
Frequently Asked Questions (FAQs)
How long does Dacromet coating last?
Dacromet-coated parts typically last 20-25 years, depending on environmental exposure and usage.
Can Dacromet coating be applied to all metals?
It is most effective on steel and iron. Other metals may require special surface treatments for better adhesion.
Is Dacromet coating environmentally safe?
Yes, Dacromet coating is zero VOC, REACH, and RoHS compliant, making it a safe choice for eco-friendly construction applications.
Looking for high-performance protection for your construction fasteners and industrial parts? Get in touch with us today!